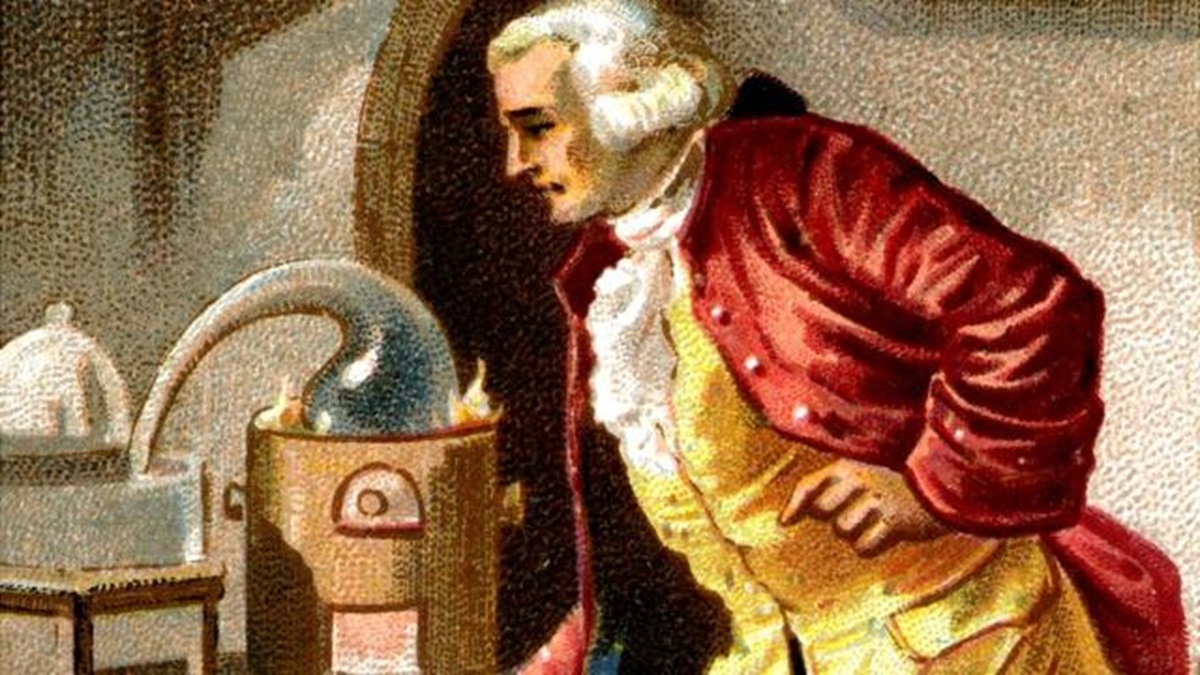
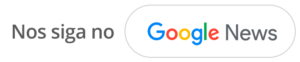
Para reduzir o ferro, seria preciso tirar o oxigênio do mineral, coisa que já se fazia empiricamente desde o início da Idade do Ferro.
Contribua usando o Google
O carvão
A descoberta do oxigênio deu-se no século XVIII por Lavoisier. Até então, imperava a teoria do flogisto de Georg Ernst Stahl, que seria um elemento químico com massa negativa. Isso explicava por que a ferrita (FE2O3) ganhava massa ao ser calcinado em forno sem ar. Para Stahl, a ferrita perdia flogístico cuja massa era negativa, ficando a massa remanescente mais elevada. Para Lavoisier, isso era uma tremenda bobagem, pois, para cada m³ de ferrita calcinada, sobravam somente 0,25 m³ de ferro, ou seja, a massa específica aumentava, mas o volume caía mais que proporcionalmente. Só por volta de 1780 é que se entendeu que a queima nada mais era do que por oxigênio onde não havia, o que poderia ou não transformar-se em calor consoante a velocidade da reação. Foi então que se descobriu que a água era um óxido, assim como a hematita e a imensa maioria dos minerais. Assim, para reduzir o ferro, seria preciso tirar o oxigênio do mineral, coisa que já se fazia empiricamente desde o início da Idade do Ferro.
Dá para deduzir que todos os metais, uns mais outros menos, combinam-se ao oxigênio que se encontra livre na atmosfera. Essa avidez por oxidar-se chama-se DQO, ou demanda química por oxigênio. Como “na Natureza, nada se perde, nada se cria, tudo se transforma”, o processo de redução do ferro requer um elemento com DQO mais elevado e que seja barato. É aí que entra o carvão que, quando colocado juntamente com minério de ferro em um forno sem ar externo, também conhecido como forno redutor, retira dele o oxigênio para sua própria queima, emitindo dióxido de carbono.
Claro que o processo é infinitamente mais complexo do que se apresenta aqui. É que intenção não é ministrar um curso de engenharia metalúrgica, mesmo porque este autor não está habilitado para isso. Assim, é melhor ater-se ao fato de que, grosso modo, o ferro é reduzido com o emprego do carvão por ser o desoxidante de obtenção mais barata. Seria possível, como já se faz em alguns casos, usar o hidrogênio em seu lugar, mas o custo de obtenção desse elemento é muito mais alto, sequer compensando o fato de que se consegue a redução em temperatura muito mais baixa. Esse carvão pode ser mineral, como a hulha da Grã Bretanha, ou oriundo de compostos orgânicos, sendo o mais abundante a madeira. Só que o carvão, mineral ou vegetal, contém contaminações que impactam negativamente a qualidade do ferro obtido. O alto teor de enxofre, por exemplo, inviabiliza o uso de nosso carvão para esse fim, obrigando o Brasil a importar 78% de seu consumo dos Estados Unidos, da Rússia, da China e da Austrália. Segundo o Ibran (Instituto Brasileiro de Mineração) em 2019, importaram-se 21 t milhões de carvão, sendo 11 t milhões de coque, que é o carvão já depurado e apto para ser adicionado às pelotas de sínter e ir para o forno. Isso custou, no mesmo período, US$9 bilhões.
Os outros 22% vêm da madeira, especialmente o eucalipto, que é o de maior absorção de carbono da atmosfera. Só que ão se pode introduzi-la diretamente nos fornos siderúrgicos. Primeiro, é preciso extrair o carbono dela, num processo de redução muito parecido com o da siderurgia em si. Nâo há que não tenha visto os fornos carvoeiros no interior, em que se põe a madeira para queimar num forno sem aberturas e fecha-se a porta, evitando que mais oxigênio entre. Como a madeira é um hidrato de carbono, o hidrogênio vai-se transformar em água, restando o carvão. Claro que o processo para alta produção é muito mais sofisticado. A necessidade de substituir o carvão mineral não renovável, pela madeira, totalmente renovável, fez com que o rendimento desses fornos subisse de 30% para 34% nos últimos dez anos. É insuficiente para torna-lo competitivo, apesar de o carvão vegetal ser de muito mais fácil de transformar em coque, do que o mineral, mas seu uso gera o que se convencionou chamar de aço verde, em que o Brasil é campeão. A Vallourec, Usina Atlas e a Aço Verde são exemplos disso.
Só que ainda não existe um diferencial preciso de preço para o aço verde perante o obtido com carvão mineral. Talvez por isso ainda não tenha aparecido uma empresa que adquira os resíduos vegetais de lavouras perenes como café, laranja entre outras, que ainda são queimados no campo após a erradicação, em vez de os aproveitar como carvão vegetal de baixo custo para a siderurgia.
Na próxima semana, o tema será como transformar vantagens comparativas em vantagens competitivas na siderurgia.
LUIZ ALBERTO MELCHERT ” JORNAL GGN” ( BRASIL)
Luiz Alberto Melchert de Carvalho e Silva é economista, estudou o mestrado na PUC, pós graduou-se em Economia Internacional na International Afairs da Columbia University e é doutor em História Econômica pela Universidade de São Paulo. Depois de aposentado como professor universitário, atua como coordenador do NAPP Economia da Fundação Perseu Abramo, como colaborador em diversas publicações, além de manter-se como consultor em agronegócios. Foi reconhecido como ativista pelos direitos da pessoa com deficiência ao participar do GT de Direitos Humanos no governo de transição.